The Art and Science of Forming Processes in Manufacturing
- Krunal Rajput
- Jun 1, 2023
- 2 min read
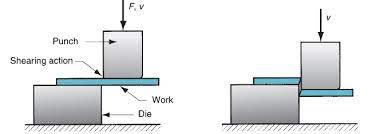
In the realm of manufacturing, forming processes play a vital role in shaping raw materials into functional and aesthetically pleasing products. From simple bends to complex contours, these processes involve the transformation of materials through the application of force, heat, or a combination of both.
This article delves into the world of forming processes, exploring their various techniques, applications, and significance in modern manufacturing.
Understanding Forming Processes:
Forming processes encompass a wide array of techniques used to shape materials, including metals, plastics, composites, and ceramics. These processes can be broadly categorized into two main types: bulk forming and sheet metal forming.
Bulk Forming Processes:
Bulk forming processes involve the deformation of a workpiece's entire volume. Common techniques in this category include forging, extrusion, and rolling.
a. Forging: A process where compressive force is applied to deform and shape a heated or cooled workpiece. It enhances the material's strength, eliminates defects, and imparts desirable properties.
b. Extrusion: A process that forces a heated or cold material through a die to create a desired cross-sectional shape. Widely used in the production of pipes, rods, and profiles.
c. Rolling: A process that passes a material through a set of rollers to reduce its thickness or modify its shape. Used extensively in the production of sheet metal, plates, and structural sections.
Sheet Metal Forming Processes:
Sheet metal forming processes focus on transforming flat sheets or coils of metal into desired shapes and structures. Some commonly employed techniques include bending, deep drawing, and hydroforming.
a. Bending: The process of deforming a sheet metal workpiece by applying force to create a desired angle or shape. Bending is widely used in industries like automotive, aerospace, and construction.
b. Deep Drawing: A process where a flat sheet is formed into a three-dimensional shape by drawing it into a die cavity with a punch. Commonly used in manufacturing kitchenware, cans, and automobile body parts.
c. Hydroforming: A technique that utilizes high-pressure fluid to shape sheet metal into complex geometries. It offers design flexibility, weight reduction, and enhanced structural integrity.
Applications and Significance:
Forming processes are essential in manufacturing industries for a multitude of reasons:
Design Flexibility: Forming processes allow manufacturers to create a wide range of shapes, sizes, and intricate details, enabling the production of diverse products to meet market demands.
Material Optimization: By carefully selecting forming processes, manufacturers can optimize material usage, reducing waste and minimizing production costs.
Strength and Durability: Certain forming processes, such as forging, can significantly enhance the mechanical properties of materials, improving their strength, toughness, and durability.
Mass Production: Many forming processes are compatible with high-volume production, making them suitable for mass manufacturing of products like automotive components, consumer electronics, and household appliances.
Cost Efficiency: Forming processes often offer cost advantages over alternative techniques, providing economical solutions for producing parts with complex geometries or low-volume requirements.
Conclusion:
Forming processes are a cornerstone of modern manufacturing, enabling the transformation of raw materials into functional and aesthetically pleasing products. Through a variety of techniques, manufacturers can shape metals, plastics, composites, and ceramics to meet the ever-evolving demands of diverse industries. Understanding the principles, applications, and significance of forming processes empowers manufacturers to optimize production, create innovative designs, and deliver high-quality products to the market.
Comentarios